Overlooked Cutter Costs in Waste Shredding: Up to 30% of Operating Expenses
In solid waste processing, multi-stage shredding systems offer robust performance, but a closer look at long-term operations reveals a significant challenge: cutter and accessory costs can escalate to represent 30% or more of total annual expenses. These costs, driven by frequent repairs and replacements, directly impact profitability and efficiency.
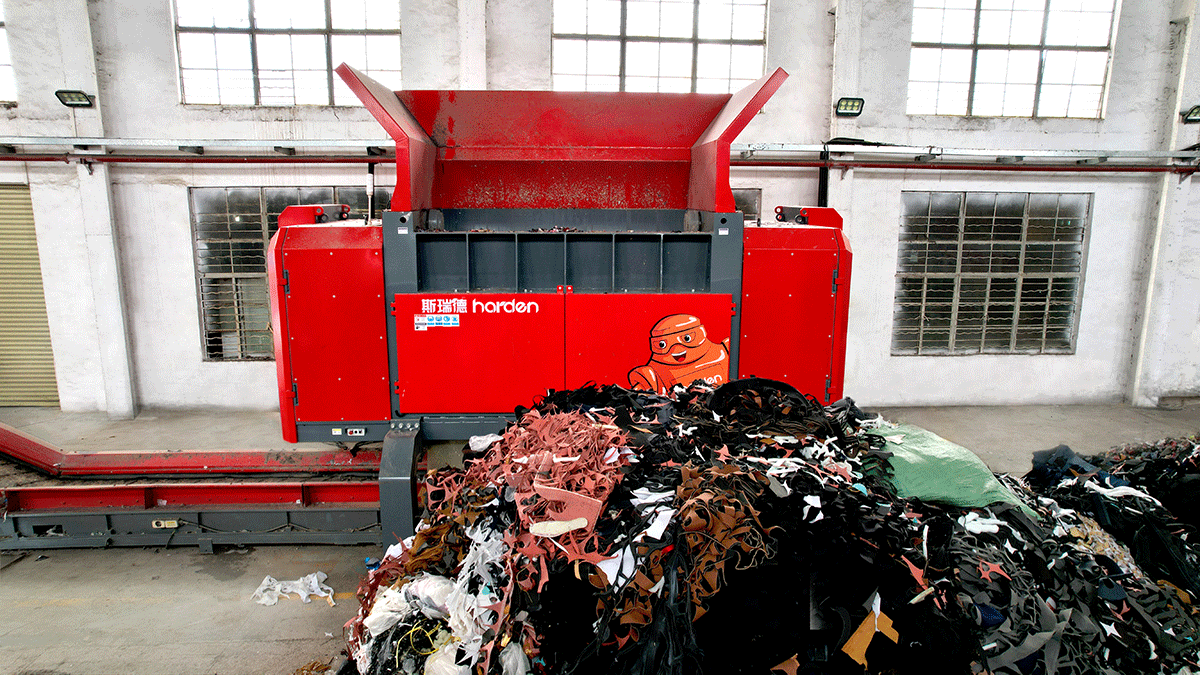
A case study from a three-year-old waste treatment facility illustrates this. Their multi-stage system's cutter-related expenditures—including replacements—totaled $170,000 annually. This equates to a 30% share of operating costs, steadily increasing year-over-year. Notably, maintenance and repair activities accounted for 86% of these cutter costs.
Such expenses arise from the inherent demands of multi-stage configurations, encompassing cutter procurement, routine upkeep, and periodic replacements. Each phase amplifies operational burdens, compressing profit margins in an industry where downtime equates to lost revenue.
1. Cutter Procurement: High Costs from Specialized Variety
Multi-stage shredders necessitate distinct cutters for primary, secondary, and fine shredding. This requires maintaining separate inventories for non-compatible tools, inflating initial investments and spare parts stockpiling to ensure uninterrupted throughput and prevent production halts.
2. Cutter Maintenance: Escalating Hidden Costs Due to Complexity
Wear varies across shredding stages, complicating repairs and demanding specialized skills. This leads to extended downtime, higher labor inputs, diverse consumables, and elevated training needs—subtle yet substantial factors that compound overall expenses.
3. Cutter Replacement: Downtime as a Major Profit Drain
Replacement procedures in multi-stage systems are labor-intensive, often involving 3-5 technicians. The entire process takes at least 1-2 days, and up to a week in some cases. Beyond direct costs for tools and materials, the resulting production stoppages translate to forgone output and amplified inefficiencies.
Breaking the Cycle: One-Step Shredding for Optimized Cost Control
Harden Machinery's one-step shredding technology presents a compelling alternative, leveraging a precision-engineered spindle system to achieve fine output sizes below 50 mm in a single pass. By utilizing one unified cutter set, it eliminates the need for stage-specific tooling, significantly reducing procurement outlays.
Engineered with high-strength alloys, precision heat treatment, and integrated digital frequency intelligence, these cutters enhance durability and adaptability across diverse waste streams.
The modular multi-row angled cutter design streamlines maintenance and replacements, enabling faster interventions that minimize operational disruptions and preserve high throughput.
Harden prioritizes total cost of ownership (TCO) in our single-shaft shredder designs, ensuring equivalent or superior shredding performance while substantially lowering cutter-related burdens. This approach not only bolsters economic viability but also supports environmental goals through efficient resource recovery.
In the solid waste sector, cutters are pivotal components influencing energy consumption, capacity, and workforce allocation. Sustainable strategies shift focus from initial purchase prices to comprehensive TCO evaluations, fostering long-term operational resilience.
For more insights on our shredding solutions, explore our product lineup or contact our team.