Paper Mill Pulper Ropes: From Waste to Resource
In the paper manufacturing process, when waste paper is processed in a hydrapulper, light impurities such as wire, plastic, string, and cotton yarn are entangled by the ragger, forming a dense, rope-like waste known as paper mill rope waste, also referred to as pulper ropes.
This complex material typically comprises approximately 40% wire, 55% paper mill waste, and 5% pulp residue. The high strength and toughness of wire make it resistant to tearing or shredding, while the flexibility and ductility of plastic cause it to wrap around shredding equipment, hindering operations. These properties make paper mill rope waste a challenging material to process.
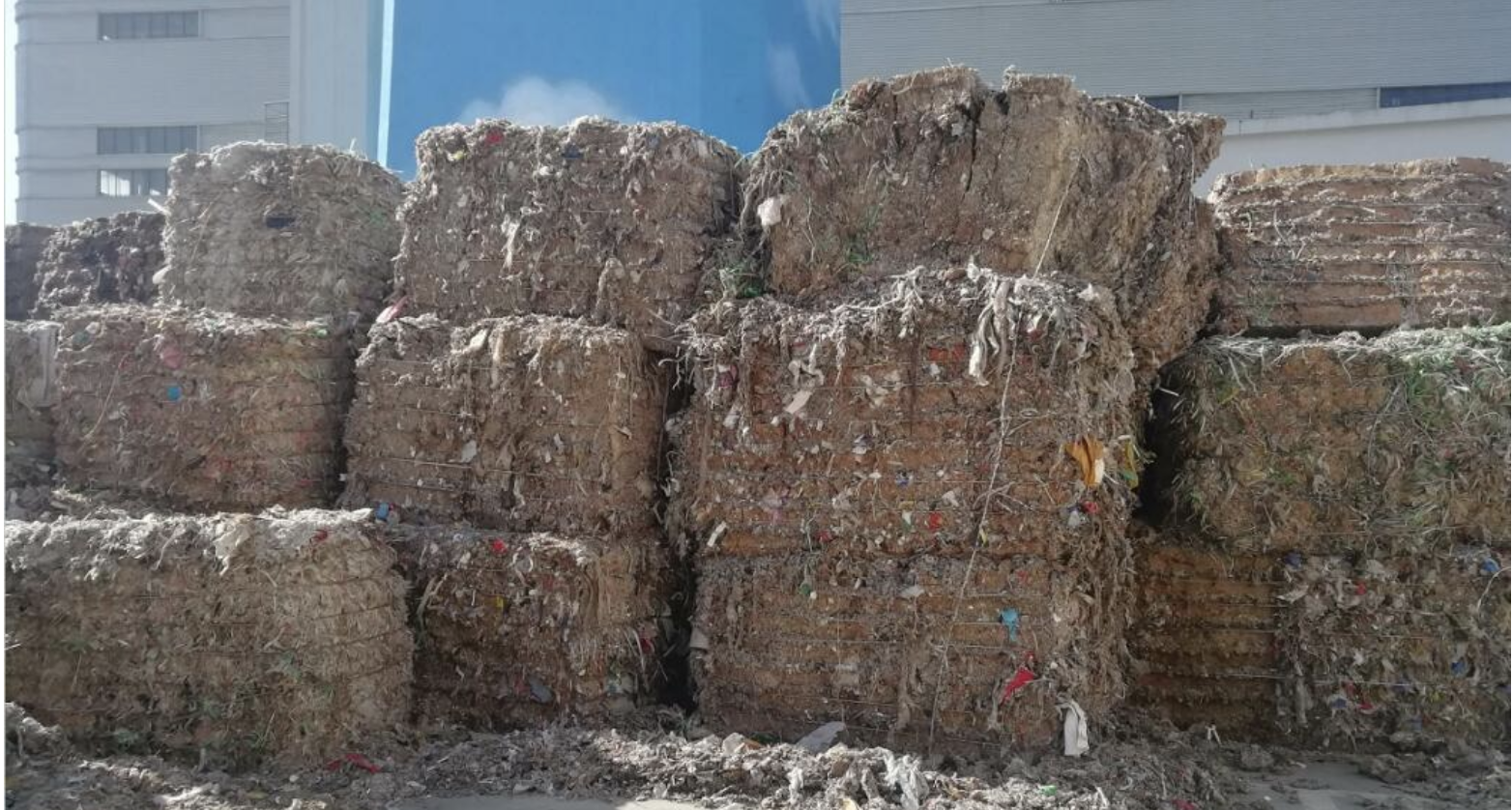
At Harden, we transform this difficult waste into a valuable resource through advanced solid waste processing solutions. Below, we outline the key steps in converting paper mill rope waste into a high-value alternative fuel, showcasing our innovative approach to waste management.
1. Pre-Shredding
This robust machine uses powerful shearing and tearing forces to reduce the waste into 80-120 mm fragments. A subsequent Secondary Shredder further refines the material to 30-50 mm, preparing it for efficient sorting and resource recovery.
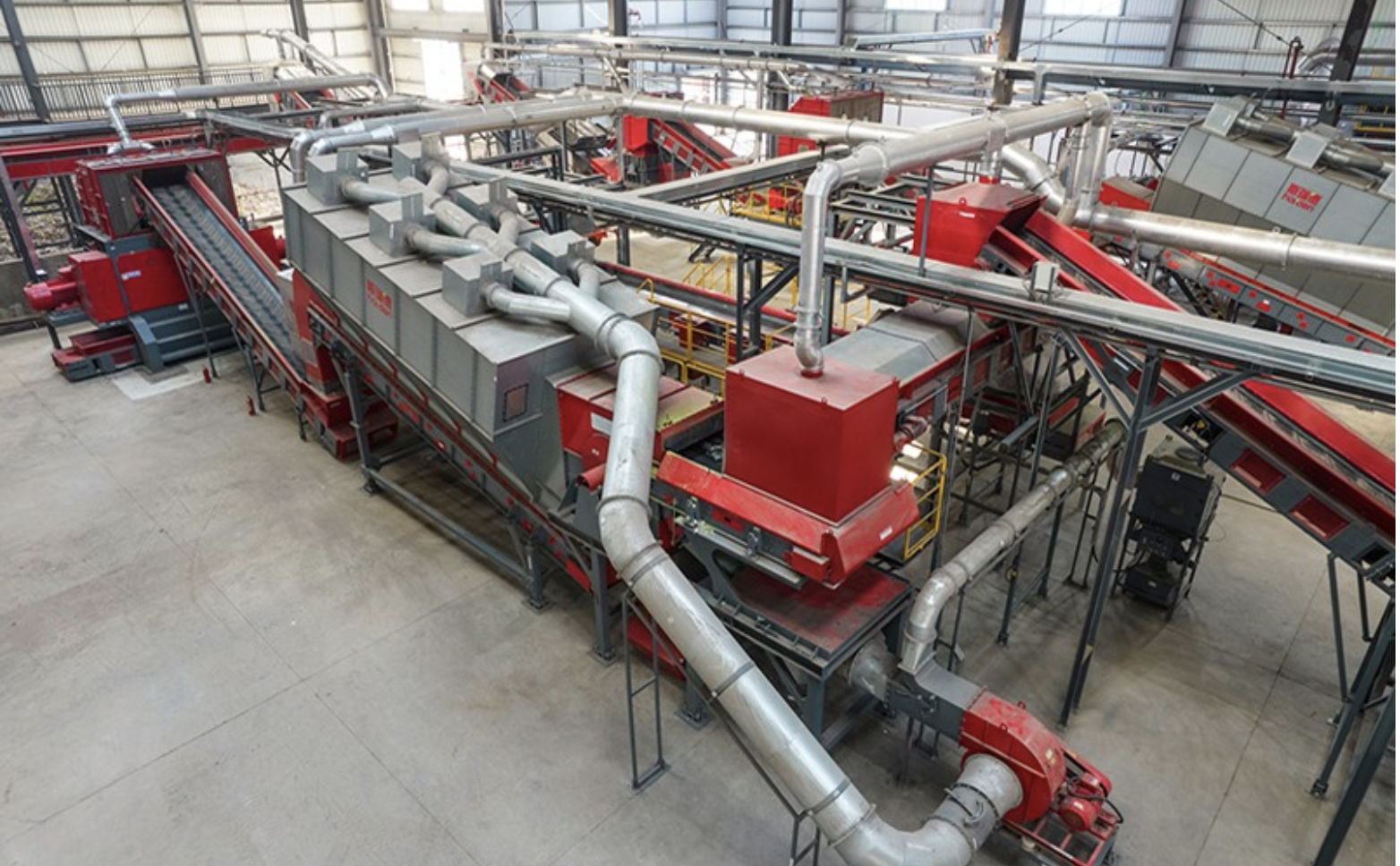
To enhance recycling efficiency, an intelligent Windshifter separates non-ferrous metals and heavy inert materials (e.g., grit, 3D materials) from the lighter combustible fractions. This precise sorting ensures high-purity outputs for downstream processing.
This process reduces reliance on fossil fuels, lowers emissions, and delivers significant environmental and economic benefits.
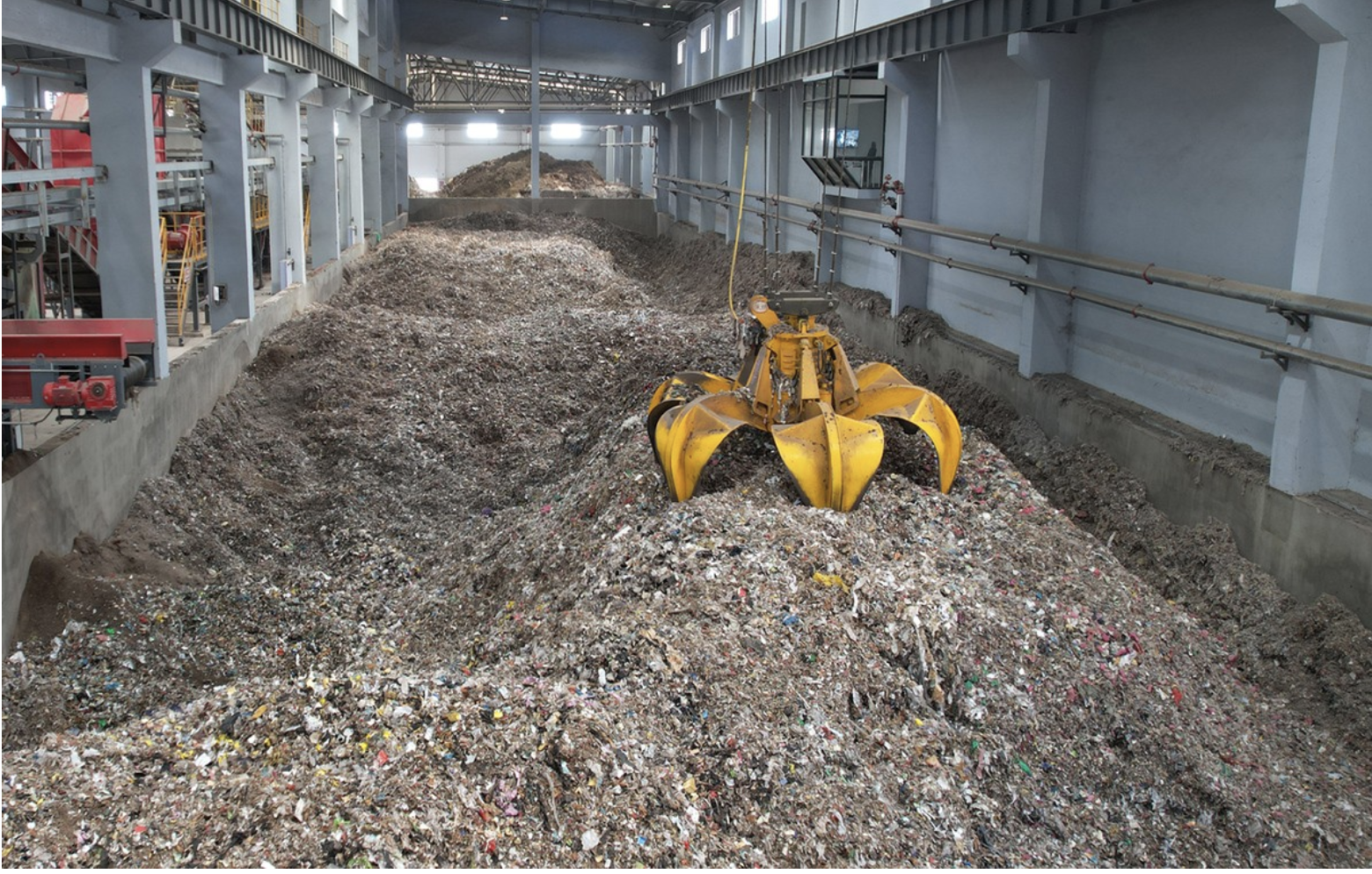