Biomass Blending Technology Sparks a Green Revolution in Coal-Fired Power Plants
Coal-fired power plants are gearing up for a green revolution by planning to incorporate at least 10% biomass fuel into their systems, which will enhance energy efficiency and reduce carbon emissions. This shift, supported by innovative co-firing techniques and advanced preprocessing technologies, positions biomass as a critical component in the move towards more sustainable energy generation.
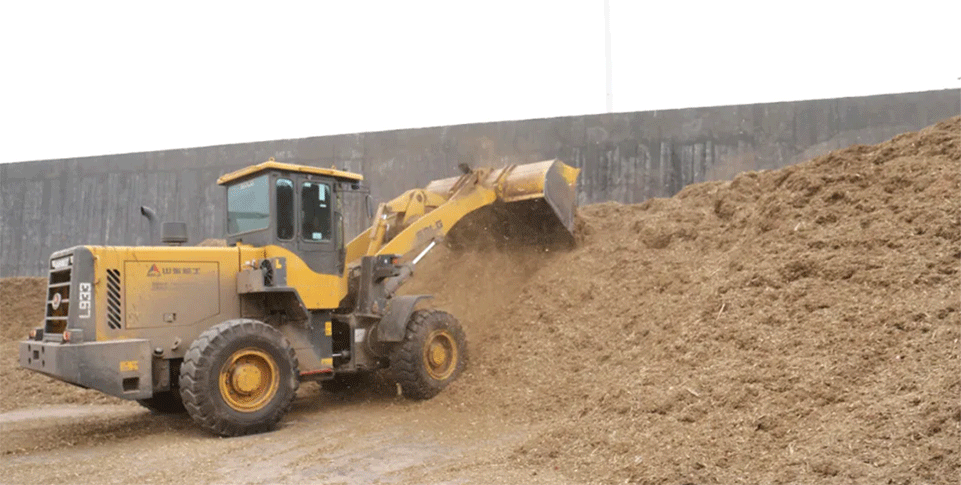
Biomass Blending Technology Sparks a Green Revolution in Coal-Fired Power Plants
In response to growing global demands for energy efficiency and carbon emission reductions, coal-fired power plants are on the brink of a significant green revolution. Recent reports indicate that, in the coming years, these facilities aim to incorporate at least 10% biomass fuel into their existing coal systems. This shift not only addresses pressing environmental concerns but also marks a substantial advancement in coal utilization efficiency and cleaner energy production.
Selecting and Preprocessing Biomass Fuel
The first step in effectively implementing biomass co-firing modifications is to identify the types and forms of biomass fuel. Options include agricultural residues like straw, forestry waste, and organic kitchen waste. By selecting biomass resources based on local availability and production, power plants can minimize transportation costs and environmental risks. The form of biomass—whether in chipped wood, pellets, briquettes, or powder—will affect blending efficiency and preprocessing expenses, significantly influencing the design and execution of modification plans.
Innovative Biomass Co-Firing Techniques
Direct Co-Firing Technology: This method involves mixing preprocessed biomass directly with coal and delivering it to the furnace. This approach, primarily adopted in the UK, has seen successful transitions from biomass co-firing to complete biomass energy generation in larger coal plants.
Indirect Co-Firing Technology: Here, biomass waste is gasified into biomass gas, which is then injected into coal-fired boilers. Germany leads the world in biomass gasification technology, supported by clearly defined subsidies under its Renewable Energy Law (EEG).
Biomass-to-Methanol Production: Utilizing agricultural waste and kitchen scraps for biogas production, this method further processes the gas into methanol—a carbon-negative solution regarded as a “zero-carbon” energy source. Sweden, with the world's largest green methanol production line, exemplifies this innovation.
Advancements in Biomass Preprocessing Technology
Crucial to the success of biomass blending is efficient preprocessing technology. In response to challenges faced by traditional methods—such as poor material compatibility and low production efficiency—Harden has developed a versatile biomass preprocessing system designed to accommodate a range of biomass feedstock.
Harden emphasizes the importance of optimizing processing solutions based on regional variations in biomass resources. This approach not only effectively addresses local biomass waste management issues but also significantly reduces coal consumption and carbon emissions, creating a win-win scenario for both economic and environmental outcomes.
As the world moves toward achieving carbon peak and carbon neutrality, biomass fuels represent a key component of this transformation in industrial sectors. Their potential to contribute to renewable energy generation is critical in addressing global energy shortages sustainably.
With the maturation of biomass co-firing technologies, the green revolution in coal-fired power generation is imminent, paving the way for a more sustainable future on a global scale.