Embracing Biomass Co-Firing: A Pathway to a Low-Carbon and Sustainable Future
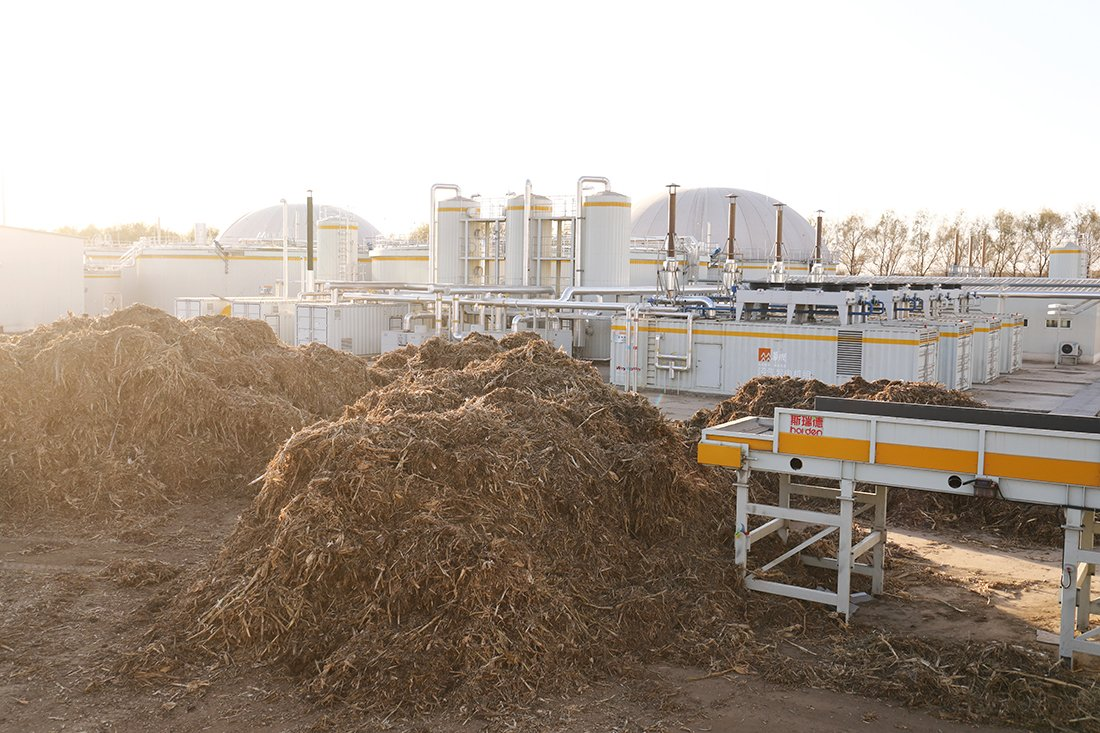
Overview and Trends in Biomass Co-firing
Biomass co-firing is the practice of partially substituting coal with biomass in coal-fired boilers for electricity generation. This method leverages biomass’s renewable energy advantages while concurrently decreasing coal use and lowering greenhouse gas emissions.
With an increasing global emphasis on reducing greenhouse gas emissions, biomass co-firing has emerged as a widely embraced low-carbon energy technology. Global energy development trends indicate strong market potential for biomass co-firing. Numerous countries, especially the United States and various European nations, have initiated pilot projects and implemented biomass co-firing in large coal power plants.
Going forward, technological advancements and supportive policies are anticipated to further broaden the application of biomass co-firing, with significant deployment expected by 2030.
Advantages of Biomass Co-firing
Lowering Carbon Dioxide Emissions
Biomass is recognized as a carbon-neutral fuel, as the carbon dioxide produced during its combustion is part of the atmospheric carbon cycle. Consequently, its carbon emissions are considered relatively neutral. Co-firing biomass alongside coal can notably reduce carbon dioxide emissions. Research shows that greenhouse gas emissions can decrease by 5% to 18%, dependent on the biomass proportion used in combustion.
Decreasing Pollutant Emissions
Beyond reducing carbon dioxide emissions, biomass co-firing effectively lowers other pollutants. The lower sulfur content in biomass compared to coal results in reduced sulfur dioxide (SOx) emissions. Additionally, its reduced nitrogen content helps decrease nitrogen oxides (NOx) generation, minimizing acid rain. Studies indicate that NOx emissions from biomass-coal co-firing have been cut by approximately 30% in various demonstration projects.
Economic Advantages
A notable benefit of biomass co-firing is its potential to lower fuel costs. In many areas, biomass is an economical and renewable energy source, often offering a lower unit heat cost than coal. This makes biomass co-firing a promising strategy for reducing operational expenses in power plants. For example, the Tennessee Valley Authority in the United States has estimated that utilizing biomass fuel in its Colbert Plant can yield annual savings of around $1.5 million in fuel expenses.
Sustainable Energy Supply
Biomass co-firing not only helps reduce reliance on fossil fuels but also opens new market opportunities for the agriculture and forestry sectors. Agricultural by-products and forestry waste can serve as valuable fuel sources, addressing waste management and combustion challenges.
Biomass Co-firing Technologies and Implementation Strategies
The primary methods for biomass co-firing include:
Direct Co-firing
This is the most cost-effective and widely utilized method. Biomass is processed using the same milling equipment as coal, and it is then directly fed into the boiler. Biomass can either be blended with coal at the fuel storage area or sent separately into the combustion chamber. Multi-fuel fluidized bed boilers display efficiency rates over 90%, and due to their lower combustion temperatures, they produce fewer emissions than traditional grate combustion methods.
Indirect Co-firing
In this configuration, biomass undergoes gasification first, with the resulting gas used in the main boiler. This process can involve cooling and cleaning the gas, which introduces challenges and higher operating costs. However, this method provides greater fuel flexibility. Several power stations, including the Zeltweg plant in Austria, the Lahti plant in Finland, and the AMER-8 plant in the Netherlands, have adopted such systems. Since gasification occurs separately, the ash from coal and biomass is also separated. This allows for a wider range of biomass fuels to be used, as issues related to varying chemical compositions and physical traits of the biomass are resolved before the gas reaches the main combustion chamber, maintaining boiler efficiency.
Parallel Co-firing
In parallel co-firing, biomass is combusted in a separate boiler to generate steam, which is then utilized alongside the main fuel for electricity generation. This method is particularly prevalent in the pulp and paper sector, where dedicated biomass boilers process bark and waste wood. These industries enhance their energy efficiency and conserve resources by effectively using the biomass residues and by-products produced in their primary operations - paper manufacturing.
Importance of Pretreatment in Biomass Co-firing
Pretreatment is essential in the context of biomass co-firing. Given the typically high moisture content and lower heating value of biomass fuels, their combustion performance tends to be inferior compared to coal. Thus, suitable pretreatment can substantially improve their heating value and stabilize the combustion process.
Increase in Heating Value
By reducing the moisture content of biomass, pretreatment boosts its heating value. The drying process is the most common form of pretreatment, which markedly lowers moisture levels and enhances combustion stability.
Enhanced Combustion Stability
Biomass fuels that have undergone pretreatment can blend more effectively with coal during combustion, leading to improved stability. The design of burners and fuel mixing ratios critically affect combustion efficiency in large-scale power plants. Pretreatment facilitates better compatibility of biomass with coal, preventing incomplete or uneven burning.
Reduction of Ash Accumulation
The burning of biomass fuels can generate significant ash, adversely impacting boiler thermal efficiency and possibly damaging equipment. By pretreating biomass to lower impurities and ash content, the total ash produced post-combustion can be reduced, thereby improving boiler efficiency.
Biomass Pretreatment Technologies for Co-firing
Once the biomass raw materials and co-firing methods are established, the choice of biomass pretreatment technology becomes vital for effective co-firing. Due to the diverse sources and complex compositions of biomass, pretreatment is essential, irrespective of the co-firing method chosen, to enhance efficacy and results.
Harden Machinery RDF Biomass Resource Processing System
Harden Machinery has performed extensive testing on various biomass types, including straw, waste bamboo, and branches with differing moisture levels. They have continually optimized their equipment guided by the principles of "finer shredding, faster separation, and more precise selection," leading to a biomass resource processing system adaptable to multiple biomass raw materials.
Harden's Project Case Studies
A biomass gasification power initiative in Northeast China utilized corn, wheat, and rice straw as raw materials. Through meticulous processing methods, different straw varieties were transformed into biomass fuel with particle sizes under 30mm and impurity levels below 5%, suitable for anaerobic fermentation and gasification power generation.
The biomass co-firing project at a cement kiln in Southwest China, incorporated local agricultural and forestry waste, such as waste bamboo and straw, to produce RDF alternative fuel for industrial kilns, substituting coal.
Biomass co-firing is growing in popularity as a vital method for energy utilization due to its environmental benefits, economic advantages, and support for sustainable development. With ongoing technological progress, especially in pretreatment techniques, the effectiveness and stability of biomass co-firing are poised for further improvement. The Harden biomass RDF solution exemplifies an advanced pretreatment method with significant potential to enhance biomass co-firing outcomes.
Looking ahead, biomass co-firing is expected to assume an increasingly important role in the global energy landscape, offering valuable solutions to the challenges of climate change and energy shortages.