Conversion of Municipal Solid Waste to Refuse-Derived Fuel: Opportunities and Challenges for the Cement Industry
The annual generation of municipal solid waste (MSW) worldwide has exceeded 2.01 billion tons and is projected to increase to 3.4 billion tons by 2050. Each year, the per capita waste generation rate is 0.74 kilograms, with approximately 33% of municipal solid waste not being effectively and environmentally managed. Currently, most urban solid waste is either landfilled or illegally dumped. Landfilling not only occupies a significant amount of land resources but also produces methane gas (CH₄), a greenhouse gas with a global warming potential 34 times greater than that of carbon dioxide (CO₂).
These disposal methods are unsustainable as they lead to land scarcity, soil pollution, and water source contamination, while also threatening marine ecosystems. Statistics indicate that 38 of the 50 largest landfills globally have been identified as indirect sources of ocean pollution, resulting in marine life deaths and exacerbating coastal erosion.
To address this issue, refuse-derived fuel (RDF) serves as a viable alternative. By extracting and converting the recyclable and combustible components from municipal solid waste into dense solid fuel (RDF), it is possible to effectively reduce landfill amounts and provide resources to the cement industry that can replace fossil fuels. This process not only reduces the environmental impact of solid waste but also provides a new fuel source for energy-intensive cement production.
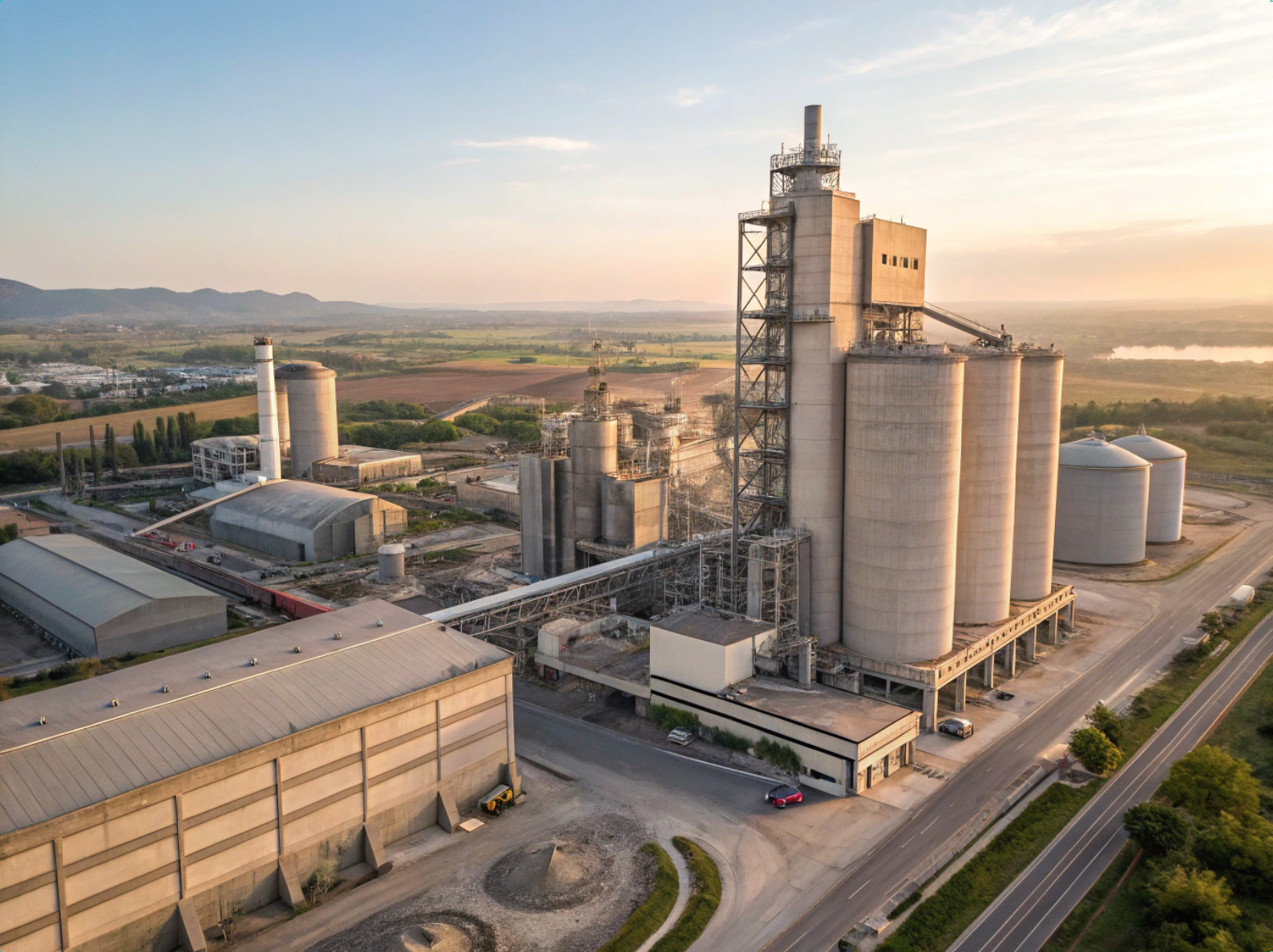
The cement industry is a major source of energy consumption and carbon emissions globally. Cement production requires high temperatures exceeding 1450°C, which consumes a substantial amount of energy (approximately 3000-6500 MJ per ton of cement) and generates a significant amount of carbon dioxide (CO₂) emissions (around 0.9 tons of CO₂ is released for every ton of cement produced).
Approximately 50% of CO₂ emissions in cement production come from the high-temperature calcination process, where limestone (CaCO₃) is converted to lime (CaO), releasing CO₂ as a predominant byproduct. Additionally, burning fossil fuels (such as coal) is also a significant source of CO₂ emissions in cement production.
With the volatility of prices for traditional energy sources like coal, cement companies face immense cost pressures, leading to an urgent demand for alternative fuels. Refuse-derived fuel (RDF) has emerged as a significant option to replace traditional fossil fuels. RDF has a higher calorific value and, during combustion, results in lower emissions of carbon dioxide, nitrogen oxides (NOx), and sulfur oxides (SOx) , thereby mitigating negative environmental impacts.
Using RDF as a substitute fuel for cement production not only helps reduce operational costs but also decreases greenhouse gas emissions, making it a feasible path toward low-carbon cement production.
Preparation and Characteristics of RDF
RDF is a dense solid fuel obtained from the combustible parts of municipal solid waste through physical pretreatment processes such as shredding, grinding, screening, air classification, and magnetic separation. The aim of this process is to separate as many recyclable materials from the waste as possible, reduce the moisture content of the waste, and ensure it has stable combustibility, thereby simplifying the subsequent handling, transportation, and storage processes.
Common pretreatment methods include source separation and mechanical separation, which can effectively reduce harmful components in the waste and enhance the quality of the final fuel.
The calorific value of refuse-derived fuel is typically comparable to that of traditional fossil fuels. For instance, RDF made from paper and plastics has a calorific value of approximately 25.02 MJ/kg, while the calorific value of rubber from car tires can reach up to 35.60 MJ/kg. Through refined processing techniques, RDF not only provides a stable source of thermal energy but also reduces the emission of environmental pollutants, particularly in cement kilns, significantly lowering NOx and SOx emissions.
Applications of RDF in the Cement Industry and Environmental Benefits
In the cement industry, the use of RDF as an alternative fuel brings significant environmental benefits. First, the carbon emissions from RDF are lower than those from coal and other traditional fuels. Generally, the CO₂ emissions from RDF are lower, and due to its lower sulfur content, using RDF can effectively reduce SOₓ emissions.
Moreover, the nitrogen content of RDF is relatively low, around 1.20%, meaning its contribution to NOₓ generation is minimal. In cement kilns, using RDF can lead to significant reductions in NOₓ emissions, with expectations of around a 17% decrease.
Furthermore, the use of RDF can reduce reliance on non-renewable resources like coal and maximize the recovery of energy from waste. By substituting traditional fossil fuels, the cement industry can not only achieve resource savings but also reduce landfill volumes and diminish the negative environmental impacts of landfilling.
Therefore, the usage of RDF presents substantial environmental prospects and is an important step toward the green transformation of the cement industry.
Harden RDF Alternative Fuel Preparation System
Harden Machinery Ltd. has designed and manufactured an efficient RDF preparation system suitable for various types of solid waste materials, such as waste fabric, leather scraps, waste plastics, and paper mill light slag.
Harden's RDF system utilizes refined crushing, intelligent air classification, and strong magnetic separation processes, enabling efficient separation of combustible materials from impurities, thus yielding high calorific value RDF fuel.
The resulting RDF is small in size, low in impurities, and high in calorific value, effectively replacing traditional coal and other high-carbon-emission fuels, reducing thermal losses in the cement production process, and minimizing fluctuations in cement kiln operations, while also having minimal impacts on cement quality.
The Harden RDF system not only improves the efficiency of waste processing but also provides a sustainable fuel option for the cement industry, reducing energy costs and lowering environmental burdens. Through the large-scale application of RDF, cement companies can not only transform solid waste into valuable resources but also achieve green and low-carbon production.